Compact DWDM laser Temperature
[09-13 17:03:11] 来源:http://www.88dzw.com 控制技术 阅读:8666次
文章摘要:Abstract: A complete and very compact thermal control solution for DWDM (Dense Wavelength Division Multiplexing) laser modules can be made using a MAX8520/21 and a single op amp. Because DWDM uses multiple lasers on a single fiber, careful control of the laser output frequencies is required. This de
Compact DWDM laser Temperature,标签:计算机控制技术,工厂电气控制技术,http://www.88dzw.comAbstract: A complete and very compact thermal control solution for DWDM (Dense Wavelength Division Multiplexing) laser modules can be made using a MAX8520/21 and a single op amp. Because DWDM uses multiple lasers on a single fiber, careful control of the laser output frequencies is required. This design can easily provide the level of performance needed for 25GHz channel spacing making it an ideal foundation for designers working on DWDM fiber optic systems.
A complete and very compact thermal control solution for DWDM (Dense Wavelength Division Multiplexing) laser modules can be made using a MAX8520/21 and a single op amp. Because DWDM uses multiple lasers on a single fiber, careful control of the laser output frequencies is required. A 1548nm DWDM system with 25GHz-channel spacing requires the laser frequency to be held at the center of the 25GHz band. The laser modules must be tuned to mid-band by changing their operating temperature and then held over all time and environmental variations. Because the laser driver can typically change 0.1nm/°C (25GHz/°C) a temperature controller with a stability of at least ±0.1°C is required. This keeps the modulated laser spectrum in the center (±2.5GHz) of the band and limits channel cross talk to a minimum. Venders are promising as many as 160 channels on a single fiber.
Because the laser modules must be set to their mid-band by changing their operating temperature from 15°C to 35°C, and the ambient can vary from 0°C to 70°C, the controller must be capable of heating and cooling. Peltier Thermal-Electric Coolers (TECs) can perform this function but the power driver for the cooler must be capable of bi-directional (both heating and cooling) operation. Furthermore, the driver must not exhibit dead-band or hunting during the transition from heating to cooling modes. The MAX8520/21 is a bi-directional power driver capable of sourcing and sinking up to 1.5 Amps. Using the MAX8520/21 with a temperature monitor (10kΩ thermistor) inside the laser module and a single op amp, a Proportional Integral differential (PID) controller can be implemented as a thermal regulation loop. The circuit block is shown below in Figure 1. A full schematic and parts list can be found at the end of this application note.
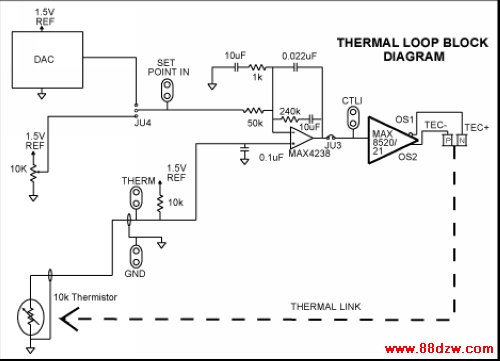
Figure 1. Block diagram for thermal control loop.
In this circuit, JU4 can be configured with a DAC (Digital to Analog Converter) or a potentiometer to set the reference temperature voltage. The op amp then compares the temperature reference voltage against the thermistor voltage and the difference is amplified and fed into the MAX8520/21. The MAX8520/21 outputs a current to reduce the error sensed by the op amp, completing the loop. Because the MAX8520/21 requires a ±1.5 volt signal at CTLI to produce ±1.5 Amps, the op amp must generate this signal from a temperature error at the input. Setting the temperature limit to ±0.1°C, and knowing that the thermistor sensitivity is 14mV/1°C, we can calculate the required op amp gain.
With
0.1°C * 14mV/1°C = 1.4mV
and because
1.4mV * Gain = 1.5V
the op amp gain must be at least 1.1K.
Tag:控制技术,计算机控制技术,工厂电气控制技术,控制技术
《Compact DWDM laser Temperature》相关文章
- › Reverse Compatibility of the D
- › Compact DWDM laser Temperature
- › Tensilica设计流程支持Cadence Encounter RTL Compiler工具
- › 英特尔 Parallel Composer入门
- 在百度中搜索相关文章:Compact DWDM laser Temperature
- 在谷歌中搜索相关文章:Compact DWDM laser Temperature
- 在soso中搜索相关文章:Compact DWDM laser Temperature
- 在搜狗中搜索相关文章:Compact DWDM laser Temperature
分类导航
最新更新