HFAN-08.2.0: Thermoelectric Co
[09-13 17:03:14] 来源:http://www.88dzw.com 控制技术 阅读:8983次
文章摘要:The MAX1968 is a cost-effective solution for controlling TECs because it integrates the four power switches and the PWM control on a 28 pin thermally enhanced TSSOP-EP package. A metallic slug on the underside of the chip allows the package to dissipate as much as 1.9 Watts and provide bipolar +/-3
HFAN-08.2.0: Thermoelectric Co,标签:计算机控制技术,工厂电气控制技术,http://www.88dzw.comThe MAX1968 is a cost-effective solution for controlling TECs because it integrates the four power switches and the PWM control on a 28 pin thermally enhanced TSSOP-EP package. A metallic slug on the underside of the chip allows the package to dissipate as much as 1.9 Watts and provide bipolar +/-3 Volts at 3 Amps from a single 5 Volts source. Switching is selectable at 500kHz or 1MHz. Independent positive and negative output current limits and a voltage limit are integrated on the chip and can be set using external resistors. An analog control signal precisely sets the TEC current regardless of the TEC voltage. Although the MAX1968 provides a cost and size effective solution for driving a TEC, precision thermal control requires an external control loop.
For precision temperature control, a local monitor inside the TEC module sends temperature information that is compared with a reference, generating an error signal. This error signal is then amplified and sent to the TEC. The TEC then changes the local monitor temperature, completing the loop. Like any control loop, steady state accuracy is related to the DC loop gain. Because of the large thermal mass, it can take tens of seconds for the temperature monitor to respond to TEC changes. Compensation of the TEC and monitor loop can require a slow integrator to avoid oscillations and overshoot. Because the integrator requires large time constants, it can be difficult to find high value capacitors with low enough leakage to achieve high DC gain. Therefore, the smallest size integrator capacitor to achieve stability must be selected.
To begin to compensate a thermal loop, the thermal response of the TEC module must be understood. By using the MAX1968 as a driver for the TEC, the internal thermistor in the module and a network analyzer with sub hertz capacity, (like the HP3562A Dynamic Signal Analyzer), the low frequency response of the TEC module can be measured. Most laser diode TEC modules behave approximately as a two-pole system. The first pole starts at 20mHz and a second pole at 1Hz. If a network analyzer is not available, measure the DC gain and use insight to approximate the TEC response. Although this model is crude, it helps us to understand the limitations in closing the loop. Since the modules have a slow 20mHz pole a 90-degree phase shift is expected from the TEC module up to 1 Hz, there after the second pole creates a potentially oscillatory condition. The TEC response in cooling mode is shown graphically with solid lines in Figure 1. Due to the fact that TECs have a four times stronger heating capacity than cooling for the same input current, this response can vary by 6 dB. Other factors such as heat sinking, ambient temperature and heat generated internally in the module can also change the response. Modules from different manufactures can have varying responses as well.
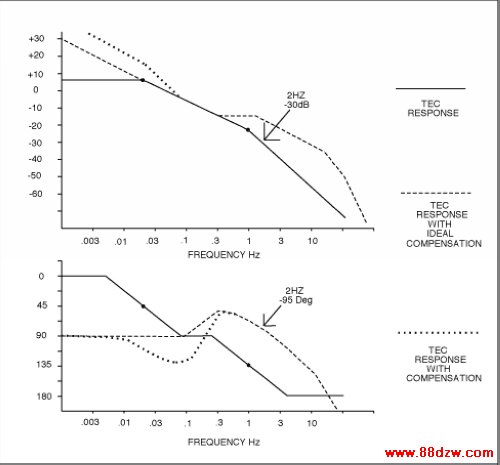
Figure 1.
The Proportional Integral Derivative (PID) controller shown in Figure 2 is a good starting point. From here, adjustments can be made to optimize the TEC response. For the highest DC gain, an integrator is needed. This integrator, formed by C2, adds a third pole which, without R3 (Figure 2), makes stability impossible. R3 inserts a zero into the integrator before unity gain crossover; ideally this should occur at the first pole, 20mHz. It can be pushed up to 70mHz without any stability issues. Although this creates a second order response from 20mHz to 70mHz, the phase never reaches oscillatory conditions (180 Degrees). This is shown with bold dotted lines in Figure 1.
Tag:控制技术,计算机控制技术,工厂电气控制技术,控制技术
《HFAN-08.2.0: Thermoelectric Co》相关文章
- › HFAN-08.2.0: Thermoelectric Co
- 在百度中搜索相关文章:HFAN-08.2.0: Thermoelectric Co
- 在谷歌中搜索相关文章:HFAN-08.2.0: Thermoelectric Co
- 在soso中搜索相关文章:HFAN-08.2.0: Thermoelectric Co
- 在搜狗中搜索相关文章:HFAN-08.2.0: Thermoelectric Co
分类导航
最新更新